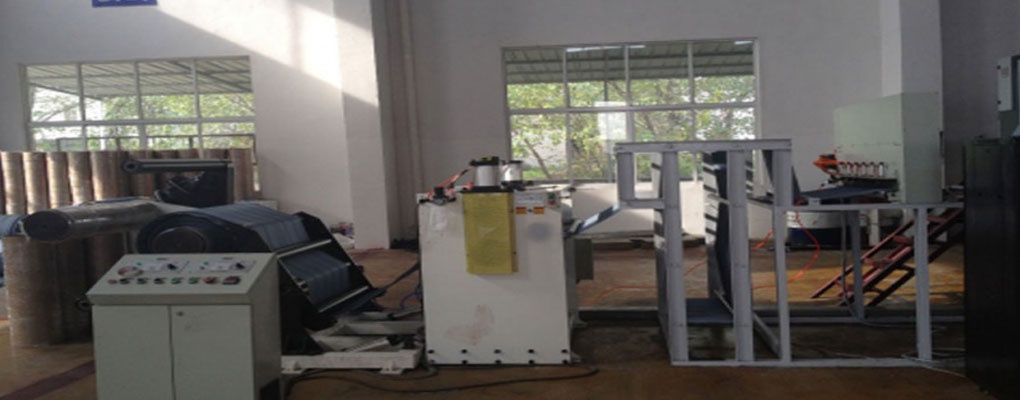
蓄电池隔板孔洞检测案例
1、 行业概况
中国铅酸电池行业自上世纪80年代以来蓬勃发展,市场需求不断扩大,技术不断革新,制造水不断提高,到目前为止,铅酸电池始终占有行业的主导地位,隔板是介于蓄电池正负极之间既能防止正负极短路又能保证离子导电的部件。它性能的优劣直接影响蓄电池的放电容量和充放电循环寿命,其重要不亚于极板本身,目前普遍使用PE隔板,是高分子材料制品,生产过程主要是挤出拉伸而成,单位平方内孔洞的数量是衡量PE隔板的质量的重要指标,为此大部分的厂家在生产环节都包含了隔板孔洞检测的设备。
2、 设备概况
生产线连续生产中,成品需要在成卷之前检测,是一个连续的过程,时时在线检测,并且进行标记,方便在以后的裁切过程中,有标记的说明有孔洞,需要在制作蓄电池的过程中剔除不使用,以保证蓄电池的性能。
孔洞检测的基本原理如下图:
说明:本系统采用机器视觉技术对薄膜质量进行检测,机器视觉检测系统一般由以下几个部分组成:照明单元、相机单元、图像采集单元、图像处理单元、计算机、显示单元、执行单元和报警单元,如下图所示。
3、 系统方案设计
限于检测对象运动的特殊性,采用工业线阵相机,行频能够满足要求,采用日本尼康公司高性能镜头,配合LED光源,通过加装编码器检测运动速度触发相机,能使隔板稳定的成像。
稳定的成像以后通过采集板卡,传输成像给计算机,进行算法运算,先对图像进行二值化,然后采用Blob分析技术,可靠性也比较高,记录孔洞的位置,传输给PLC,PLC再控制打印标记气缸,进行孔洞标志打印。熟练的应用了现代的计算机技术。
为了保证系统高速相应,每套视觉系统配备一台工控机,同时为了保证监测到的孔洞时时保留记录打印,又配备了一台工控机。系统控制的原理框图如下:
4、 上位机软件编程
系统采用了板卡,需要把信号读入windows,利用windows接口函数,及通讯函数,读取相机的数据,上位机采用visual studio 2008 C++ 开发,系统主要界面如下:
5、 设备照片
6、 工程结论
系统容工业自动化技术,机器视觉,计算机软件编程,网络组态为一体,是一个难度比较大的项目,通过我们的努力目前系统已经满足生产的需要,并且随着生产规模的扩大,二线,三线的配套系统已经在洽谈开发当中。